INVESTIGATING FIBER:
THE ENVIRONMENTAL IMPACT OF TEXTILES AND MATERIALS
This research encompasses the environmental impacts of a handful of textiles and dyes. The lifecycles of cotton, polyester, rayon, and fabric dye are investigated and analyzed.
NOVEMBER 2019
COTTON
What it is: Cotton is a natural fiber that comes from the plant Gossypium. Grown from the outer layer of the cotton plant's seeds, cotton is the most produced natural fiber on earth. It has been around for thousands of years; the oldest cotton fiber recorded estimated from 5000 B.C.
Where’s it Made: Most of the world's cotton comes from the U.S., China, and India. China has 7,500 textile companies, which produce $73 billion of cotton cloth annually. India produces 6,423 thousand metric tons of cotton every year, while Florida, Mississippi, California, Texas, and Arizona are the major cotton-producing states in America.
How it is Made: According to barnhardtcotton.net, the best season to grow cotton is Spring, most farmers plant cotton seeds in April. The temperature of the soil affects the maturity and growth of the cotton seeds, so it’s important to plant cotton when the soil is warm. Cotton seeds are sown in fields once weeds and unwanted plants are removed; special pesticides and fertilizers are used to ensure the best quality product. The harvesting is done through a machine in which the cotton takes the shape of a ball. To make cotton threads into fabric, the raw cotton gathered from the fields is cleaned of dirt and leaves before being fed into a cotton gin. These machines clean and dry cotton for a second time before the fibers are plucked from the cotton seeds. These individual fibers are overlapped and twisted around each other, and longer fibers are more valuable than short ones, because they require less overlap and can be woven into finer threads. Finally, these fibers are spun and woven into fabric.

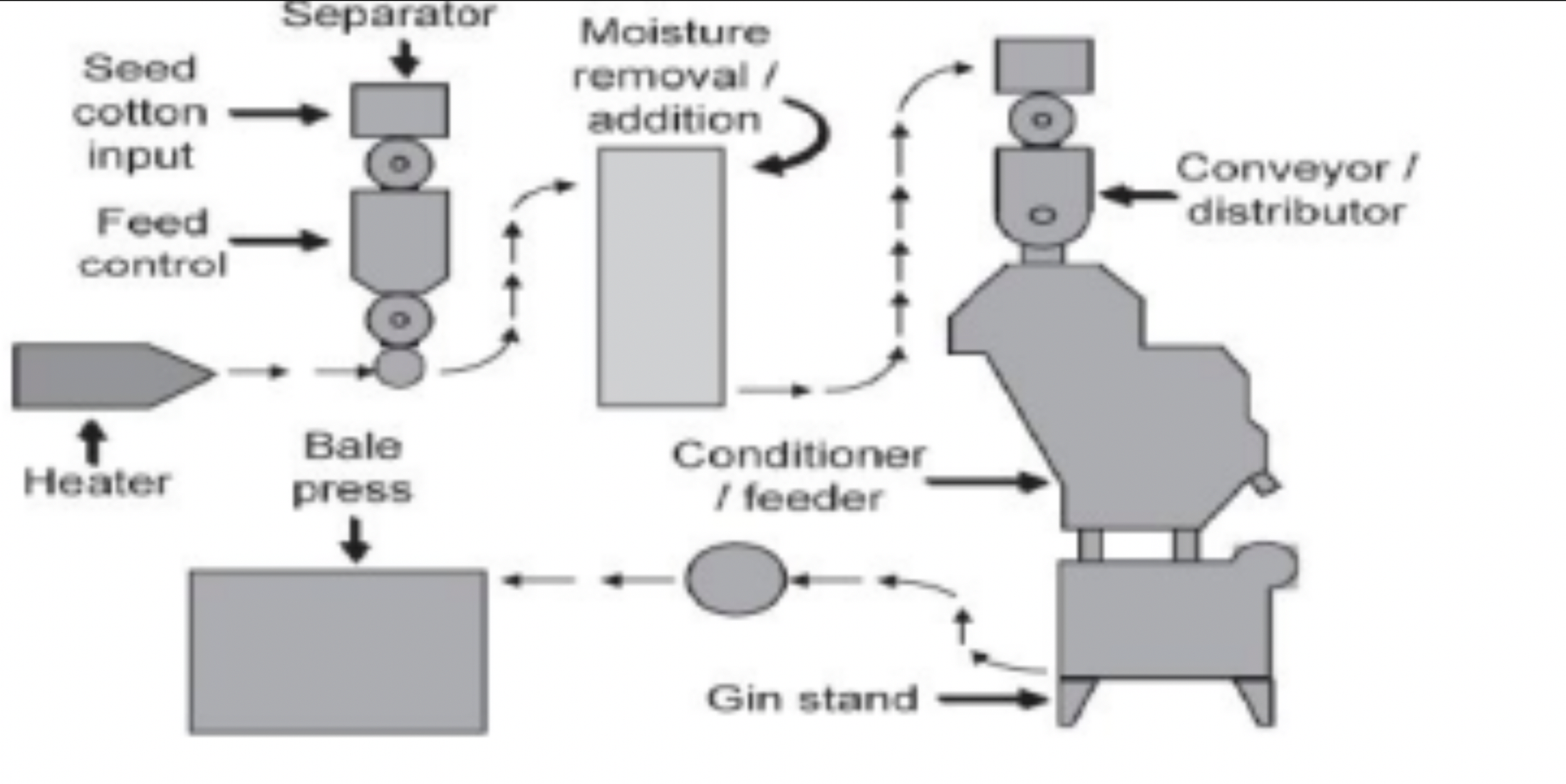
Environmental Factors in Transportation/Shipping: According to eurosender.com, cotton is widely produced throughout the world. As a result, a specific shipment processes is implemented to ensure that cotton can be spread on a wide scale. Once cotton is harvested, it is pressed into cotton bales. This process requires a baling press machine that squeezes cotton into cotton bales (the average size of a cotton bale is 500 pounds). Once cotton is pressed into bales, it gets covered in shipment materials consisting of a cotton cloth or plastic for protection.
What can one bale of cotton make?
215 Jeans
249 Bed Sheets
690 Terry Bath Towels
765 Men's Dress Shirts
1,217 Men's T- Shirts
1,256 Pillowcases
3,085 Diapers
4,320 Mid-Calf Socks
21,960 Handkerchiefs
Care/Lifespan: Lifespan of cotton depends on the length of the fiber. Different fiber lengths are utilized for specific products and expectancy of durability. Longer fibers are used to make towels, bandages, and wallpaper while shorter fibers are used for dynamite, photographic film, and rayon. Cotton has many different purposes, so its specific lifespan is ultimately determined by how it is used and how carefully it is cared for.
Decomposition: Cotton can take about five to six months for cotton to fully decompose. Since cotton is a natural fiber it is biodegradable, which helps microorganisms break them down easier.
Major Environmental Issues: Cotton has earned the title of being the dirtiest crop in the world, consuming insecticides and producing pesticides that tarnish the soil and threatens the growth of crops. Cotton crops contaminate surrounding water with pesticides and fertilizer. Water scarcity is also an issue; one kilogram of cotton needs 20,000 liters of water- this equates to one pair of jeans or a cotton t-shirt.
How Much Goes to Waste: It is inevitable that clothing will end up in landfills due to excess and improper disposal of their unwanted garments. Cotton is an affordable fabric making it a popular fiber choice in fast fashion. Clothing consumer culture motivates fast fashion companies to produce higher output resulting in clothes that aren’t properly disposed of. There are over 16 million tons of textiles that end up in landfills. The average person disposes about 80 pounds of clothing per year. Unfortunately, cotton farming is responsible for 24% of insecticides and 11% of pesticides that contaminate soil and water.
How Companies Are Reducing Waste: Companies like Patagonia are reducing textile waste by repurposing cotton scraps. Ecotec is another company that uses recycled yarn made from pre-dyed cotton which reduces water consumption by 80%. Companies recognize that recycling cotton fiber and regulating water consumption can make an impact if done right. By recycling scraps or reusing cotton, companies can mitigate the amount of textiles that end up in landfills.
Alternative Solutions: Growing organic cotton can make a big difference. There are no toxic chemicals that go into the soil, air, or water. 88% of water is reduced, and 62% of energy is reduced, along with the reduction of insecticides and pesticides. Additionally, growing organic cotton promotes a safer work environment for farmers and their families who live near these crops. Organic cotton can be an affordable fiber if the demand continues to increase.

POLYESTER
What it is: Polyester is a notoriously strong fabric resulting from a chemical reaction between petroleum, air, and water. There are several different kinds, the most well-known being polyethylene terephthalate (PET), but all forms of polyester are made of long polymers. These are comprised of an ester (a simple chemical compound), a dihydric alcohol, and terephthalic acid. Experts from Plastics Insight add that the synthetic polymers found in polyester can be made from “petroleum-derived ethylene glycol.” To put it simply, polyester consists of plastic made from oil.
Where it is Made: The demand for polyester has been on the rise since the 1990s, placing a high demand on factories, specifically in Asia. According to IHS Markit, “Production of polyester fiber has migrated to Asia, which now accounts for 94% of global capacity.” This isn’t too surprising considering the booming textile industry in Asia and the high demand for polyester in China, which is currently the largest consumer of polyester fabrics based on the most recent available data. In the future, however, some production is expected to move to less-developed countries in Asia, such as Vietnam and Bangladesh, in reaction to rising wages in China. Other big players in the production of polyester include India and Southeast Asia, who continue to pay less for labor.
How it’s Made: Melted down PET plastic chips are spun into polyester fibers. Polyester is a manufactured synthetic fiber made using a chemical reaction typically conducted in a vacuum at high temperatures. According to Craftech Industries, a process called “polymerization” occurs when, “A petroleum by-product, alcohol, and carboxylic acid are mixed to form a compound known as monomer or ‘ester.’” The material produced by polymerization (usually a kind of PET plastic) is then cut into chips, melted down, and then extruded through spinnerets to produce melt-spun fibers. These fibers are then left to harden and stretched into the longer fibers that make up polyester. This is known as “drawing.” In other words, PET plastic is melted down to produce new plastic fibers. It should also be noted that this production process requires a lot of water so that fibers can cool properly. In fact, according to waterfootprint.org, “the water footprint of polyester can be as high as 71,000 cubic metres per tonne of fibre,” due to wasteful production methods. It has also been found that more than 66% of polyester production sites have high levels of water scarcity and water pollution, further proving the effect polyester production has on water supply. Additionally, the petroleum used to produce polyester has to be drilled out of the ground using vehicles that also require oil to function. This petroleum is then taken by additional vehicles that require additional fuel to be turned into a textile. According to Forbes, this makes it so that it takes more than 70 million barrels of oil to make polyester every single year, which places an incredible strain on the environment.
How Much is Produced: The amount produced each year has been shooting upwards in recently, with the most recent available data from statista showing that the world produces about 53.7 million metric tons annually (including what is recycled). This is up 9.7 million metric tons from 2012.
Lifespan and Care: The durability of polyester fabric means it’s easy to care for and long lasting. Despite its environmental issues, polyester is versatile and usually quite cheap. Experts say it’s also strong, stretch resistant, easy to clean, and doesn’t wrinkle easily.
Decomposition Process: Polyester sticks around for a long time and pollutes the planet. The decomposition process for polyester is long and complicated. Because it’s not biodegradable, it can take anywhere from 20 to 200 years before it’s gone. It’s also comprised of petroleum, which means it pollutes the Earth once it does finally decompose.
How Much Goes to Waste: Polyester is the most commonly used fiber, making up almost 50 percent of the world’s clothes. However, only about 14% of polyester ends up recycled. China has also recently implemented a ban on importing solid waste, according to a study by Textile Exchange, which means recycled polyester production rates are likely to decrease. However, this same study explained that “Recycled polyester can also be made from other post-consumer plastic such as ocean waste or discarded polyester shirt or from pre-consumer processing residues such as fabric scraps,” which means there are many ways to take waste within the country and turn it into recycled polyester. As a whole, Americans throw away almost 13 million tons of fabric every year. When it comes to plastic, however, that number skyrockets to 26 million tons. Since its basic components are essentially plastic, polyester contributes to both of these problems, and is not going away any time soon.
Major Environmental Issues:The most pressing sustainability issues brought up by polyester production include: water scarcity, water pollution, oil pollution, and energy consumption. According to CFDA, Polyester production also ends up emitting 14.2 kg of CO2 per kg of polyester produced. In fact, in 2015, polyester ended up emitting 282 billion kg of CO2. It also sheds an estimated half a million tons of microplastics into the water each year.
Environmental Factors in Transportation/Shipping: It’s estimated that it takes about 3 megajoules (MJ) of energy to transport a piece of polyester, using trucks and lots of gasoline. Pipelines, ships, and tankers are also used to help with the transportation of the petroleum that makes up polyester. Pumping stations are also used to vent gases and remove excess fluids.
How Companies Are Reducing Waste: Some companies, such as Repreve, are utilizing recycled plastics to create their polyester. Their recycled polyester items can continued to be recycled and made into new garments.
Additional Solutions: There’s a lot we can do to reduce polyester’s environmental footprint. Girlfriend Collective is an athletic wear company that utilizes 25 recycled post-consumer water bottles in every single pair of their polyester leggings. Additionally, they have partnered with ECONYL to recycle the waste found in oceans into a unique fabric called “LITE.” They also send wastewater to a facility where it is treated to remove dyes and stray fibers before being released back into the environment, and they send leftover “dye mud” to pavement facilities where it is repurposed for paving stones and sidewalks. Apart from ecological sustainability, they also ensure that their factories pay living wages and allow for unionization.
Bionic is another sustainable company that uses ocean materials (namely plastic) to create its fabric. They have currently invented three different yarns all made from recycled plastic. Apps like “Good On You” are also useful in that they give brands ratings on their ethics and sustainability practices, to help consumers make smart, ecological choices when shopping.
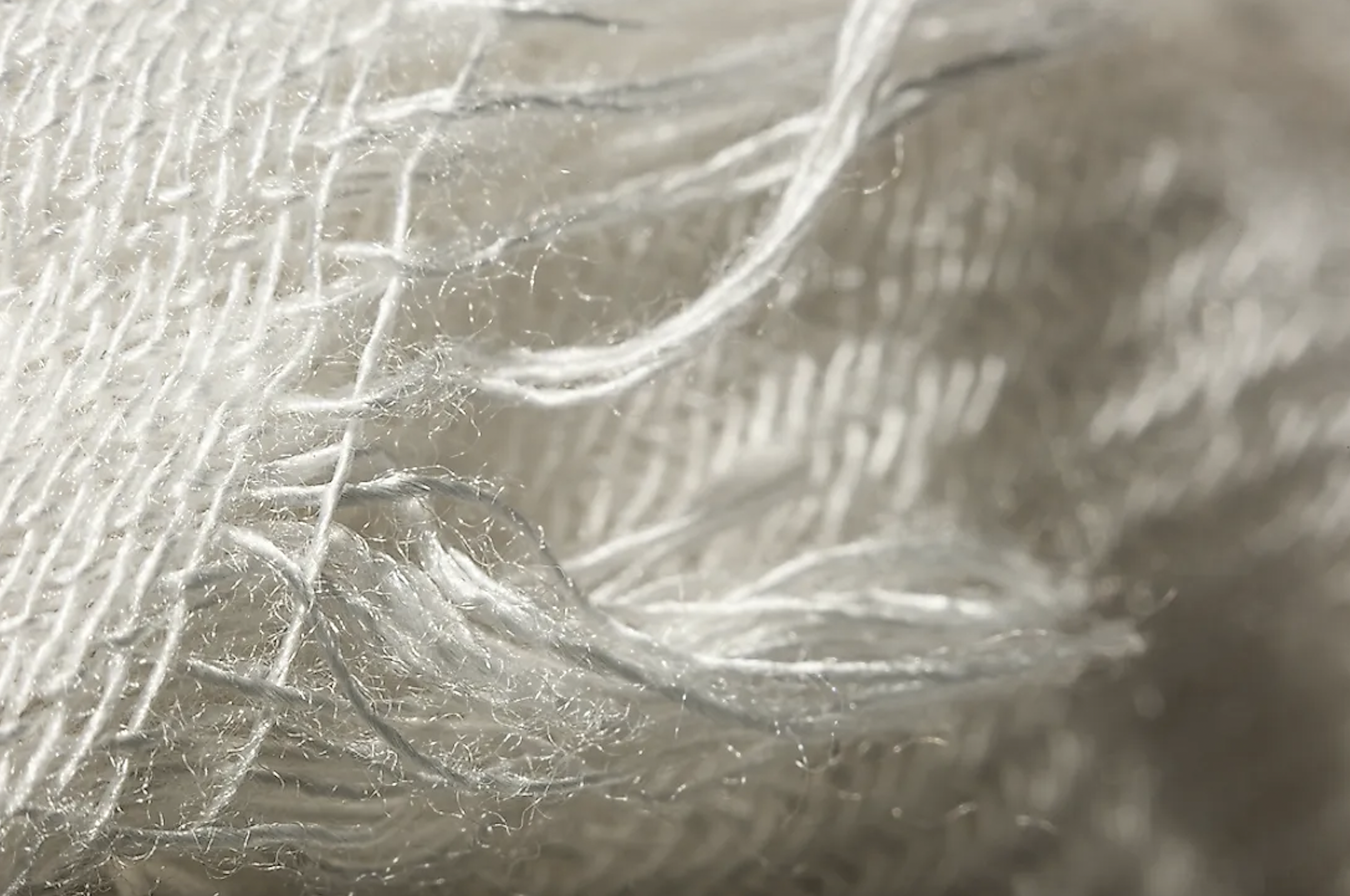
RAYON
What it is: Rayon is a semi-synthetic textile made from purified cellulose which is taken from wood pulp. Viscose rayon is derived from wood pulp from trees such as eucalyptus, pine, beech, soy, and sugar cane. This fabric is known to imitate properties of many different kinds of silk, cotton, and wool, which makes it extremely versatile for many different types of clothing. The three main types of rayon include viscose, modal, and lyocell. It was the first regenerated cellulosic fiber ever produced and was originally marketed as “artificial silk” in the US. Viscose Rayon carries the same comfort properties as natural fibers, making it versatile in its use. Rayon may also be used as a filler for furniture cushions, sleeping pillows, and stuffed toys for children. The absorbent properties of rayon have also led it to be used in adult diapers and other hygiene products. Rayon is also used as a primary component in vehicle tires, which results in a product that is less expensive than nylon tires.
Where it is Made: 24% of the world’s rayon is produced in India, but 65% of viscose fiber is made in Chinese manufacturing facilities, as well as in Japan, Germany, Brazil, and Laos.
How it’s Made: According to madehow.com, viscose rayon is produced by first, steeping sheets of purified cellulose in sodium hydroxide, which produces sheets of alkali cellulose. The sheets are dried, shredded into crumbs, and then aged in metal containers for 2 to 3 days where the temperature is carefully controlled. After aging, the crumbs are combined with liquid carbon disulfide, which turns the mix into orange-colored crumbs known as sodium cellulose xanthate. The cellulose xanthate is bathed in caustic soda, resulting in a viscose solution that looks like honey. Any dyes in the design are then added. The syrupy solution is filtered and stored in vats between 4 and 5 days. The viscous solution is next turned into strings of fibers by forcing the solution through a spinneret into an acid bath. In the acid bath, the acid solidifies the filaments, now known as regenerated cellulose filaments. Depending on the type of yarn desired, several spinning methods can be used, including Pot Spinning, Spool Spinning, and Continuous Spinning. In Pot Spinning, the filaments are first stretched under controlled tension onto a series of offsetting rollers called godet wheels. This stretching reduces the diameter of the filaments and makes them more uniform in size, and it also gives the filaments more strength. The filaments are then put into a rapidly spinning cylinder called a Topham Box, resulting in cake-like strings that stick to the sides of the Topham Box. The strings are then washed, bleached, rinsed, dried, and wound on cones or spools.
How Much is Produced: 5.8 Million Tons. According to the most recent available data, world production of viscose fabrics came in at almost 6 million tons. However, rayon currently makes up only 5 or 6% of total fibers used in the global textile industry.
Lifespan and Care: Not the longest lasting. There’s no doubt that rayon and rayon blends tend to be fairly accessible and inexpensive. However, with this cheap price tag comes a shorter lifespan. According to medium.com, generally, rayon can only last a few seasons of being washed before it starts to pill, stretch, and bag. It also absorbs moisture, which makes it even weaker. Typically, it should be dry cleaned to prevent these side effects, which means its care process can be a little more extensive than other fabrics.
Decomposition Process: According to Ecocult, in a controlled soil environment, rayon was found to decompose in about six weeks, but in a landfill, can take decades to biodegrade while releasing potent greenhouse gasses. Additionally, a study published in the Journal of Applied Polymer Science demonstrated that rayon breaks down quicker than cotton when composted. Rayon also decomposes faster than cotton in general (six weeks vs 11 weeks), due to its small microfibers. Despite its quick decomposition time, store-bought rayon has usually been washed, souced, dyed, and treated, so in most cases it will biodegrade releasing these chemicals.
Modal rayon tends to take a bit longer to decompose, needing about four months to decompose only halfway. Even with the advancements that have been made over time, most rayon manufacturing processes in use today are not considered environmentally friendly. In fact, they use a range of polluting chemicals and heavy metals. On the other hand, lyocell manufacturing, and that of Tencel in particular, is an extremely environmentally friendly process and the friendliest of these fibers according to life.ca.
Major Environmental Issues: Rayon generates undesirable water and air emissions and the processing of wood pulp leads to the use of many harsh chemicals that pollute our planet. Of particular concern is the emission of zinc and hydrogen sulfide. Additionally, according to Canopy Planet, “Dissolving-pulp (the base material for rayon/viscose) wastes approximately 70% of the tree and is a chemically intensive manufacturing process.” It is also estimated that 150 million trees are used every single year in the production of cellulosic fabric. Studies from the 1930s show that 30% of American rayon workers suffered severe effects mainly due to the release of carbon disulfide in the process. Fortunately, in the last two decades, new technologies have been deployed in the viscose manufacturing process which are highly efficient in capturing the carbon disulfide released in the manufacturing process. Leading manufacturers of viscose now apply these latest technologies in the viscose process for effective control of hazards from these chemicals.
Environmental Factors in Transportation/Shipping: Rayon generates undesirable water and air emissions in its transportation process as well, since it’s typically shipped overseas. This leads to significant consumption of energy and oil in gasoline.
How Companies Are Reducing Waste: The nonprofit organization: Canopy is partnering up with brands to “end the use of fibre from Ancient and Endangered Forests in the manufacture of viscose and rayon fabrics.” So far, Canopy has more than 170 brand partners, including Abercrombie & Fitch, Allbirds, and Reformation. Canopy also engages with rayon viscose suppliers, who can put pressure on dissolving pulp mills while also engaging the pulp mills themselves, using pressure from up the supply chain to essentially give them no choice but to comply, or lose almost all their customers. The Rainforest Action Network is also working on getting some of the most notable brands in the industry to set timely goals to protect forests and reduce waste in rayon production.
Additional Solutions: “One Million Women” is an initiative to make positive environmental change in all aspects of life. CEO Natalie Isaac wrote a book and published a website on this project which focuses on responsible ways to compost and dispose of old textiles.

DYE
What it is: The first mention of fabric dye is dated back to 2600 BC. According to the experts at Key Colour, before industrialization, dyes were made with natural pigments mixed with water and oil and were primarily used to decorate skin, jewelry, and clothing. There were many dyes sources used ranging from plants to insects to even sea life. Commonly used dyes were found near where the source was discovered, meaning different geographical locations utilized specific colors. According to Brahms Mount, a few examples were roots, berries, bark, leaves, wood, and other organic substances, such as fungi. Natural dyes were very predominant until William Perkin accidentally discovered mauveine, a rich synthetic purple in 1856, as described in Love to Know. In 1869, a decline of natural dyes began when the red dye found in Madder root was successfully duplicated synthetically. Ace UK accounts for the fact that many other colors followed, and today, 90 percent of clothing is dyed synthetically. Unfortunately, synthetic dyes are used so heavily in the textile industry that it is possible to tell the next season’s hue by the color of the rivers in China.
Where it’s Made: According to Business Wire, the largest global producer of synthetic dyes by region is Asia followed by North and South America and Europe. By country, China is the largest producer, followed by India, the US, Brazil, United Kingdom, and Germany. China has become the world’s major textile producer, accounting for nearly 55% of total global fiber consumption and now accounts for 40-45% of world dyes consumption. China and India are also major exporters of dyes. Is it likely that consumption of dyes will decrease in China because of rising labor costs and environmental concerns; the Chinese government has been forcing polluters to limit or cease operations to meet environmental laws. The textile dye market size, in 2019, is estimated at $8.2 billion, and is predicted to grow to $10.9 billion by 2024. This is due to an increase in demand for textile dyes for the textile industry (Markets and Markets, 2019).
What is it (Classification): Dyes are classified in many different ways, from their chemical compositions to the types of fibers they are applied to, even the method of application. Fabrics’ fibers react differently to dyes. Some dye molecules attach to the surface of the fiber, others get absorbed by the fiber, others interact with the fiber’s molecules. The Society of Dyers and Colourists (SDC) and the American Association of Textile Chemists and Colorists (AATCC) classify dyes by their chemical composition.
They recognize the following dyes: acid, azoic, basic, direct, disperse, pigment, reactive, sulfur, and vat. Love to Know shares an extensive description of these dyes:
Acid dyes: water-soluble dyes applied to wool, silk, nylon, modified rayon, certain modified acrylic, and polyester fibers. This process results in bright colors with complete color range but, colorfastness varies.
Azoic dyes: The fiber is impregnated with one component of the dye, followed by treatment with another component, forming the color. Colorfastness in this process is excellent. Basic dyes: The results are bright but have poor colorfastness; they have limited use on cellulosic and protein fibers.
Direct dyes: This method of dye is soluble and has an affinity for cellulose fibers. An electrolyte is added to the dye bath to control the absorption rate of the dye by the fiber.
Disperse dyes: This was first developed to dye acetate fibers. Hydrophobic fibers have little affinity for water-soluble dyes, making disperse dyes the best method to dye acetate and polyester.
Pigment dyes: Dye that has insoluble coloring particles. Pigments are added to the spinning solution of synthetic fibers and become an integral part of the fiber.
Reactive dyes: Dyes combine with fiber molecules either by addition or substitution. This method was first introduced to the industry in 1956.
Sulfur dyes: This dye is insoluble but become soluble in sodium polysulphide. This method is low cost and is easy to apply.
Vat dyes: Dyes that are insoluble in water but become soluble when reduced in the presence of an alkali. The term vat dye is derived from the large vessels used to apply the dye.
How it’s Made: First Source Worldwide describes how natural dyes come from nature through organic and inorganic sources. Today, some of the most popular options for natural dyes are indigo, turmeric, and onion shells. Natural dyes have little affinity for textile materials, they require fixing-agents known as mordants. These agents are essential in providing intensity and brightness to the colors produced and also enhanced the fastness properties of dyes. The dyeing process has always been a key factor in successful trading of textile products. When thinking about the products we have in our closet that have gone through the process of dyeing, there are a few attributes we may not be aware of: good fixation with respect to light, perspiration and washing, both initially and after prolonged used. To make sure these conditions are met, the source that provides color to the fiber must show high affinity, uniform color, resistance to fading, and be economically feasible.
Most of the dyes used today are Synthetic Organic Chemicals that derive from crude oil, known as aromatic organic compounds used to dye everything from pills to clothes,according to First Source Worldwide. These compounds are substances that consist of one or more rings that contain alternating single and double bonds. In the ring of an aromatic compound, electrons are delocalized, which means they will spread out over the entire ring and are not attached to a specific atom. Most dye molecules contain two parts: the first is a single benzene ring or a substituted benzene ring. This could also contain a system of either two rings fused together or three rings fused together. The second part is a chromophore, where the molecule is exposed to visible light and will absorb and reflect the color. The methods to dye products have not changed much over time. According to intechopen.com, water is still one of the key components, used to clean, dye, apply auxiliary chemicals to the fabric, and to rinse the treated fibers or fabrics.
There are three steps that need to be followed to dye a product:
The first is preparation, in which unwanted impurities are removed from the fabric before the dyeing process begins. This can happen by cleaning with aqueous alkaline substances and detergents or applying enzymes. Some fabrics can be bleached with hydrogen peroxide or chlorine-containing compounds to remove their natural color.
The second step is dyeing, an aqueous application of color to the textile substrates, mainly utilizing synthetic organic dyes with, usually, a high temperature and pressure of some sort. Dyes and chemical aids are applied to the fabric to get a uniform depth of color.
The last step includes treatments with chemical compounds aimed at improving the quality of the fabric and the product in general. Some of the treatments are permanent press, water proofing, softening, antistatic protection, soil resistance, stain release, and microbial/fungal protection.
How Much is Produced: According to Ace UK, it is estimated that over 10,000 different dyes and pigments are used industrially and over 735 tons of synthetic dyes are annually produced worldwide today (2016).
Lifespan and Care: Synthetics last, natural dyes don’t. If applied correctly, synthetic dyes can last for several seasons. Natural dyes, however, fade a little more quickly.
Natural vs Synthetic Dye: Phil Patterson, consultant to textile companies globally and director of UK-based Colour Connections, believes natural dyes are not the answer. As previously mentioned, natural dyes mostly come from plants, which makes them expensive since they require larger quantities to create the same depth in color, and need mordants (which have heavy metal salts in their composition) to stick to the fabric. The color also washes off over time, raising questions about the fabric’s sustainability.
“Given the complexities of creating natural dyes and the resources required, such as water and land against the vast commercial market across the globe, it’s not possible to use only natural dyes.” Patterson believes the answer lies somewhere in between natural and synthetic, a hybrid perhaps.https://www.theguardian.com/sustainable-business/sustainable-fashion-blog/2015/mar/31/natural-dyes-v-synthetic-which-is-more-sustainable
Another problem found with natural dyes is that some such as logwood and bloodroot can be toxic. Logwood can produce a wide range of colors, but its active ingredients: hematein and hematoxylin can be harmful when it enters the body through inhalation, ingestion, or skin absorption. Bloodroot can also be harmful because it may cause irritation and inflammation when inhaled. It is important to keep in mind that most natural dyes are safe and harmless, however, they can be toxic due to the mordant used for their application. Mordants can include aluminum, copper, iron, and chrome. According to keycolour.net, synthetic dyes became popular because of their lasting color and pay-off and wide range of color choices. The dyes are made up of chemical compounds that can be harmful to the human body with high exposure to mercury, lead, chromium, copper, sodium chloride, toluene, and benzene. More manufacturers are minimizing the use of harmful chemicals in their products and are more focused on creating dyes with environmentally-friendly ingredients.
Dye Waste: The global textile industry discharges over 40,000 to 50,000 tons of dye into the water system (2016). Approximately 10-15% (200,000 tons) of dyes are released into the environment during this process. Most of the time, people are more concerned with the color of the water and thus prioritize the process of removing color from wastewater than removing the colorless and soluble organic substances.
Major Environmental Issues: During the dyeing process, the dye that does not attach to the fabric is lost to the wastewater stream. One t-shirt uses 16 to 20 litres of water. Dye waste in bodies of water diminishes the photosynthetic activity of algae and has an impact on the aquatic food chain according to trustedclothes.com. A solution available to remediate the effects that dyes have on water is by enhancing the existing disposal treatment plants through Reverse Osmosis, which converts water into fresh water. Gas emissions comprise the second biggest problem for the textile industry. Even though most processes in the textile mills produce atmospheric emissions, transparency in air emission statistics are often not available, since this type of pollution is hard to sample, test, and quantify in a report. Textile dyes can cause allergies, such as contact dermatitis and skin irritation. they also contribute to respiratory diseases, such as mucous membranes or upper respiratory tract. Different types of dyes can cause different types of harm. Azo dyes have highly toxic effects, especially carcinogenic and mutagenic, which enter the body by ingestion and are metabolized by intestinal microorganisms causing DNA damage.
Environmental Factors in Transportation/Shipping: According to cargohandbook.org dyes are shipped as powder, liquid, or paste, packed in drums, barrels with inner paper bags or multi-ply bags. Some dyes can deteriorate if they come in contact with air. Soluble dyes, if wet, may cause actual loss of dye by leaching the material out of the package.
How Companies Are Reducing Waste: According to medium.com, Ecofoot has developed a more sustainable dye that reacts with cellulose fibres at lower temperatures. This technology does not require the use of salt and can dye cotton garments at low temperatures. Ecofoot Indigo is a hybrid pigment used in dyeing denim, this pigment avoids using toxic reducing agents that are traditionally used to convert indigo pigment to a water soluble form. Additionally, Intech Digital introduced a new “waterless” textile printing technology using Blackjet reactive pigment inks to provide coloration. Preservation Dyehouse works to reduce the effects of harmful dyes by using sustainable dyestuff that doesn’t irritate the skin.
Additional Solutions: Companies can invest in Cleaner Production Technologies by combining soft flow machines with low salt dyes and membrane filtration. In this switch, 50% of water consumption is reduced. Another alternative is to implement activated carbon to the dye process, which will allow for the absorption of chemicals in waste and thus reduce the amount of pollutants in the wastewater stream. Since cotton requires more water to dye than other textiles, companies could use cotton pretreatment. For instance, Dow has developed a pretreatment process called ECOFAST Pure that is applied before the dyeing process to produce cationic cotton. This technology decreases the use of dye and water by 50 percent for cotton dyeing. Colorfix also employs a synthetic biological approach by using bacteria to color textiles, which can reduce the use of water by up to 10 times.